Stretch film, currently widely used material in the transportation industry, is accepted by consumers for its convenience. The earliest domestic use of PVC as the substrate, DOA as a plasticizer, and self-adhesive production of PVC stretch film. Due to environmental protection issues, high cost (relative PE ratio, small unit packaging area), poor stretchability, etc., when the domestic production of PE stretch film began to be phased out from 1994 to 1995. PE stretch film first uses EVA as a self-adhesive material, but its cost is high and it has a taste. Later, PIB and VLDPE were developed as self-adhesive materials. The base material was mainly LLDPE, including C4, C6, C8, and metallocene PE ( MPE).
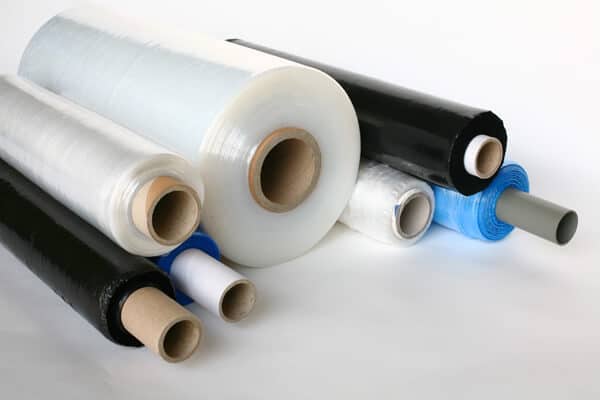
- Profile
The early LLDPE stretch film was mainly blown film, which developed from single layer to two layers and three layers. The production of LLDPE stretch film was mainly based on the casting method. The process is shown in the figure below. , High transparency and other advantages, can be applied to the requirements of high magnification pre-stretching. Because single-layer casting cannot achieve single-sided adhesion, the application field is limited. Single-layer and double-layer casts are not as extensive in material selection as three-layer casts, and the cost of the formula is high, so a three-layer co-extrusion structure is preferred. High-quality stretch films should have high transparency, high longitudinal elongation, high yield point, high transverse tear strength, and good puncture performance [1]. - Production process conditions
It adopts imported linear polyethylene LLDPE resin and tackifier special additive ratio production. It can produce multi-functional stretch film for hand use, resistance machine, pre-stretch machine, UV protection, anti-static and rust prevention. It has the following advantages: 1. Using double-layer co-extrusion equipment, the extruded stretch film can maximize all the characteristics of each polymer. Its transparency, tensile strength, and perforation resistance are optimal at the melting point. status. 2, with good tensile properties, good transparency, uniform thickness. 3. Longitudinal elongation, good resilience, good transverse tear resistance, and excellent self-adhesive overlap. 4, is environmentally friendly recyclable materials, tasteless, non-toxic, can be directly packaged food. 5. Can produce single-sided sticky products, reduce noise during winding and stretching, and reduce dust and sand during transportation and storage. - Sticky Control
Good adhesiveness makes the outer packaging film layer and layer of the goods stick together to make the goods firm. There are two main ways to obtain the adhesiveness: one is to add PIB or its masterbatch to the polymer; the other is to blend VLDPE . PIB is a translucent viscous liquid. Direct addition requires special equipment or modification of the equipment. Generally, PIB master batch is used. There is a process of PIB migration, which usually takes three days. In addition, it is also affected by temperature. When the temperature is high, the viscosity is strong; when the temperature is low, it is not very sticky. After stretching, the viscosity is greatly reduced. Therefore, the finished film is best stored in a certain temperature range (suggested storage temperature is 15 ℃ ~ 25 ℃). Blended with VLDPE, the viscosity is slightly worse, but there are no special requirements for the equipment. The viscosity is relatively stable and is not controlled by time, but it is also affected by temperature. When the temperature is higher than 30 ° C, it is relatively viscous. By adjusting the amount of adhesive layer LLDPE to achieve the desired viscosity. This method is mostly used for three-layer coextrusion.
- Control editing of physical and mechanical properties
High transparency is conducive to the identification of goods; high longitudinal elongation is favorable for pre-stretching and saves material consumption; good puncture performance and transverse tear strength allow the film to meet the sharp angle of the goods or The edges do not break; the high yield point makes the packaged goods more secure.
The film produced by the casting method has high transparency, which is not discussed here. With the increase of the number of comonomers of the material, the branch chain length increases, the crystallinity decreases, and the “twisting or kinking” effect of the resulting copolymer increases, so the elongation increases, and the puncture strength and tear strength also increase. MPE is a high stereoregular polymer with a narrow molecular weight distribution, which can accurately control the physical properties of the polymer, so there is further improvement in performance; and because of the narrow molecular weight distribution of MPE, the processing range is also narrow, and the processing conditions are difficult to control. Generally, Add 5% LDPE to reduce the melt viscosity and increase the flatness of the film.
The price of MPE is also high. In order to reduce costs, MPE is usually used with C4-LLDPE, but not all C4-LLDPE can be used with it, and there should be choices. Machine stretch films mostly use C6 and C8 materials, which are easy to process and can meet various packaging requirements. Because of the low stretch ratio of manual packaging, C4 materials are mostly used.
Material density also affects film performance. With the increase of density, the degree of orientation increases, the flatness is good, the longitudinal elongation is increased, and the yield strength is increased, but the transverse tear strength, puncture strength, and light transmittance are all reduced, so the performance of all aspects is often non-sticky. The layer was added with an appropriate amount of medium density linear polyethylene (LMDPE). Adding LMDPE can also reduce the friction coefficient of the non-adhesive layer and avoid the adhesion of the packaged pallet to the pallet.
Effect of cooling roller temperature. As the temperature of the cooling roller increases, the yield strength increases, but the remaining properties decrease. Therefore, it is generally appropriate to control the temperature of the cooling I roller at 20 ° C to 30 ° C. The tension of the casting line affects the flatness and tightness of the film. If PIB or its master batch is used as the adhesive layer, it will also affect the migration of PIB and reduce the final viscosity of the film. The tension is generally not more than 10kg. Too much stress remains in the film roll, which reduces the elongation and other properties, and easily causes film breakage. Application form of stretch film
Stretch film has a wide range of applications. It is mainly used in conjunction with pallets to package entire sets of scattered goods instead of small containers. Because it can reduce the cost of bulk goods transportation and packaging by more than 30%, it is widely used in the packaging of a variety of products such as hardware, minerals, chemicals, medicine, food, machinery, etc .; it is also widely used in the field of warehouse storage Stretch wrapping film tray packaging for three-dimensional storage and transportation to save space and space [1].
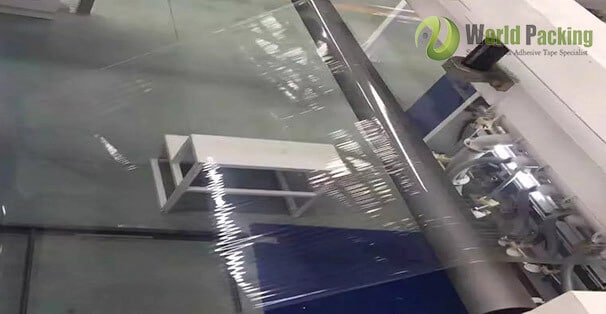
- Use
1. Sealed packaging
This packaging is similar to shrink film packaging. The film wraps the tray around the tray, and then two heat grippers heat seal the film at both ends. This is the earliest form of use of the stretch film, and as a result, more packaging forms have been developed.
2.Full width packaging
This packaging requires that the film width is sufficient to cover the tray. The shape of the tray is regular, so it is suitable for use, and the suitable film thickness is 17 to 35 μm.
- Hand-packed
This type of packaging is the simplest type of wrapping film. The film is mounted on a stand or held by hand, and the film is rotated by the tray or the film is rotated around the tray. It is mainly used for repacking after the damaged tray is damaged, and ordinary tray packaging. The packaging speed is slow, and the suitable film thickness is 15-20 μm; - Stretch film wrapping machine packaging
This is the most common and most widely used form of mechanical packaging. It is rotated by the pallet or the film is rotated around the pallet. The film is fixed on the bracket and can be moved up and down. This packaging capacity is very large, about 15 to 18 trays per hour. Suitable film thickness is about 15 ~ 25μm;
5.Horizontal mechanical packaging
Different from other packaging, the film revolves around the article, which is suitable for long goods packaging, such as carpets, boards, fiberboard, special-shaped materials, etc .; - Packaging of paper tube
This is one of the latest uses of wrapping film, which is better than old-fashioned wrapping films for paper tube packaging. Suitable film thickness is 30 ~ 120μm; - Packaging of small items
This is the latest packaging form of stretch film, which can not only reduce material consumption, but also reduce the storage space of the tray. In foreign countries, this packaging was first introduced in 1984. Just one year later, many such packaging appeared on the market. This packaging form has great potential. Suitable for film thickness 15 ~ 30μm; - Tube and cable packaging
This is an example of the application of the stretch film in special fields. The packaging equipment is installed at the end of the production line. The fully automatic stretch film can replace the strap to tie the material, and can also play a protective role. A suitable thickness is 15 to 30 μm. - Stretch form of pallet mechanism package
The packaging of stretch film must be stretched. The stretch forms of pallet mechanical packaging include direct stretch and pre-stretch. There are two types of pre-stretching, one is roll pre-stretching and the other is electric stretching.
Direct stretching is done between the tray and the film. This method has a low stretch ratio (about 15% to 20%). If the stretch ratio exceeds 55% to 60%, it exceeds the original yield point of the film, the film width is reduced, the puncture performance is also lost, and the film is very Easy to break. And at 60% elongation, the pulling force is still very large. For light goods, it is likely to deform the goods.
Pre-stretching is done by two rolls. The two rollers pre-stretched by the roller are connected by a gear unit. The stretching ratio can be different according to the gear ratio. The pulling force is generated by the turntable. Since the stretching is generated within a short distance, the friction between the roller and the film It is large, so the width of the film does not shrink, and the original puncture performance of the film is maintained. No stretching occurs during actual winding, reducing breakage due to sharp edges or corners. This pre-stretching can increase the stretching ratio to 110%.
The stretching mechanism of electric pre-stretching is the same as that of roll pre-stretching, except that the two rolls are driven by electricity, and the stretching is completely independent of the rotation of the tray. Therefore, it is more adaptable and suitable for light, heavy and irregular goods. Due to the low tension during packaging, the pre-stretching ratio of this method is as high as 300%, which greatly saves material and reduces costs. Suitable for film thickness 15 ~ 24μm.
- Features
- Unitization: This is one of the biggest characteristics of stretch film packaging. With the film’s strong winding force and retractability.
- Primary protection: The primary protection provides the surface protection of the product, forming a very light and protective appearance around the product, so as to achieve the purpose of dustproof, oil-proof, moisture-proof, waterproof, anti-theft. It is especially important that the wrapping film makes the packaging items be uniformly stressed, so as to avoid damage to the items due to uneven force, which cannot be achieved by traditional packaging methods (bundling, packing, tape, etc.).
- Compression fixation: The product is wound and packaged with the retracting force after the stretch film is stretched to form a compact unit that does not take up space. The product trays are tightly wrapped together, which can effectively prevent the transportation process. The misalignment and movement of Chinese products, and the adjustable tensile force can make hard products close and soft products shrink, especially in the tobacco industry and textile industry with unique packaging effects.
- Cost saving: The use of wrapping film for product packaging can effectively reduce the cost of use. The use of wrapping film is only about 15% of the original box packaging, about 35% of heat shrink film, and about 50% of carton packaging. At the same time, it can reduce the labor intensity of workers, improve packaging efficiency and packaging grade.
- To sum up, the application field of stretched film is very wide, but many fields in China have not been involved, and many areas already involved are not widely used. With the expansion of the application field, the amount of stretched film will definitely increase Its market potential is inestimable. Therefore, it is necessary for us to vigorously promote the production and application of stretched films [1].
Collet by Shenzhen World Packing Industrial Limited
Top Stretch Wrap Film & Adhesive Tapes Manufacturer in China
References
- Bi Changwu, Zhang Lei, Cui Kezeng. Market Analysis of China’s Stretch Wrapping Film [C] // The First Annual Meeting of the Plastic Packaging Committee of the China Packaging Federation and the New Technology Symposium on Plastic Packaging. 2006.
viagra online
WALCOME
: )